(1)顆粒物
現(xiàn)有磚瓦窯首先從工藝控制開始,減少工藝過程中顆粒物的產(chǎn)生,如窯車的清掃,窯門的雙層密封,少投或不投外燃煤;采取合理的密閉、回收工藝;然后從精細(xì)化管控減少顆粒物,如從原料燃料差異、焙燒溫度條件、風(fēng)機(jī)運(yùn)行曲線、生產(chǎn)負(fù)荷、污染治理設(shè)施情況等多方面摸索條件,實(shí)現(xiàn)企業(yè)內(nèi)部的管理減排;最后是采用末端高效除塵設(shè)施。新建磚瓦窯應(yīng)主要從合理工藝設(shè)計+高效除塵設(shè)施實(shí)現(xiàn)顆粒物減排。
適用于磚瓦企業(yè)的除塵技術(shù)有濕式除塵、電除塵或袋式除塵(配干法/半干法脫硫)。常規(guī)濕式除塵技術(shù)效率稍低,但可以和脫硫協(xié)同考慮,減少投資和運(yùn)行費(fèi)用。電除塵器效率可>95%,袋式除塵器效率可>99%。
對于磚瓦行業(yè)的高效除塵,主要是在濕法脫硫塔后加裝濕式電除塵器或在塔內(nèi)除霧器位置加裝管束除塵除霧器,可有效降低煙氣中細(xì)顆粒物的排放。濕式電除塵最早應(yīng)用在燃煤電廠,為實(shí)現(xiàn)顆粒物超低排放采用的技術(shù),后來鋼鐵行業(yè)燒結(jié)機(jī)濕法脫硫后也有很多應(yīng)用。不論是管束式除塵除霧器方案或濕式電除塵器方案,一般都需要脫硫塔煙氣出口的煙塵濃度不能超過30mg/m3。
濕式電除塵器和管束式除塵除霧器比較情況如下:
① 濕電設(shè)備投資高,管束投資在濕電的60%以下;
② 濕電系統(tǒng)復(fù)雜,系統(tǒng)增加阻力高,運(yùn)行電耗高,需增加廢水處理,增加運(yùn)行費(fèi)用,管束是濕電的50%以下;
③ 濕電場地要求高,一般單獨(dú)布置,占用場地面積大,而管束式除塵除霧技術(shù)僅稍增加脫硫塔高度即可;
④ 濕電對于細(xì)顆粒除塵效果更好,煙氣的凈化效果高于管束。
⑤ 濕電對工藝負(fù)荷變化適應(yīng)性強(qiáng)于管束。在負(fù)荷變化大時,管束式除塵除霧器可能存在運(yùn)行不穩(wěn)定的情況。
(2)二氧化硫
要優(yōu)先采取降低燃料原料中硫含量的措施,如廢氣排放仍不能達(dá)標(biāo),則要安裝煙氣脫硫設(shè)施。
適用的脫硫技術(shù):國內(nèi)有多種成熟技術(shù),可實(shí)現(xiàn)較高的脫硫效率。具體建議是,非煤矸石類:從經(jīng)濟(jì)性講,建議選用含硫量低的煤,可采用濕式脫硫除塵一體化技術(shù);煤矸石類:SO2遠(yuǎn)高于其他企業(yè),應(yīng)上高效脫硫設(shè)施,雙堿法、單堿法、石灰/石灰石-石膏、氧化鎂、干法/半干法等都可以。
脫硫方法有很多種,脫硫劑的選擇是關(guān)鍵因素之一,應(yīng)充分考慮當(dāng)?shù)乜捎玫母鞣N脫硫劑資源、運(yùn)輸條件,并結(jié)合脫硫渣的利用與處置情況、技術(shù)經(jīng)濟(jì)指標(biāo),經(jīng)綜合比選后確定。
廠區(qū)周圍有可靠來源的新鮮電石渣,宜優(yōu)選電石渣做脫硫劑;選石灰做脫硫劑時,氧化鈣含量宜>75%;選氧化鎂做脫硫劑時,氧化鎂含量宜>85%;選石灰石粉做脫硫劑時,碳酸鈣含量宜>90%。
對濕法脫硫,應(yīng)注重脫硫除霧器的選擇和應(yīng)用,一般設(shè)置在脫硫塔內(nèi),并設(shè)置便于維修的沖洗裝置,除霧器出口煙氣霧滴的設(shè)計濃度宜<75mg/m3。
對于干法/半干法脫硫應(yīng)注重脫硫廢渣處理。當(dāng)采用鈣基脫硫劑時,脫硫渣應(yīng)氧化,并考慮副產(chǎn)物的綜合利用;采用鎂基脫硫劑時,應(yīng)考慮亞硫酸鎂等回收利用。
脫硫裝置應(yīng)配備自動控制系統(tǒng),濕法脫硫應(yīng)對脫硫劑濃度、脫硫液pH值、液位、系統(tǒng)阻力、煙氣溫度、循環(huán)泵電流、物料消耗等參數(shù)進(jìn)行監(jiān)控。脫硫裝置應(yīng)按照《污染源自動監(jiān)控管理辦法》規(guī)定安裝在線監(jiān)測系統(tǒng)。
筆者對多家磚瓦窯采用的雙堿法脫硫進(jìn)行調(diào)研,發(fā)現(xiàn)難以連續(xù)穩(wěn)定運(yùn)行的原因主要有:
① 設(shè)計參數(shù)與正常生產(chǎn)狀況下煙氣排放量、煙氣濃度不一致;
② 脫硫塔內(nèi)除霧器短路或損壞,大量堿液外逸到周邊環(huán)境;
③ 企業(yè)操作水平低,憑感覺加藥,使脫硫液pH值不穩(wěn)定;
④ 石灰中有效氧化鈣含量低,“雙堿法”變“單堿法”;
⑤ 循環(huán)池體積小,池內(nèi)底渣清運(yùn)不及時,為鈉堿再生提供的空間不夠,影響脫硫效率;
⑥ 為降低成本,環(huán)保不檢查時有些企業(yè)停運(yùn)脫硫設(shè)施。頻繁啟停造成塔內(nèi)結(jié)垢堵塞情況嚴(yán)重。
脫硫系統(tǒng)在竣工驗(yàn)收達(dá)標(biāo)后,應(yīng)加強(qiáng)運(yùn)行維護(hù),特別是安裝在線監(jiān)控裝置后,如果粗放管理很難實(shí)現(xiàn)穩(wěn)定達(dá)標(biāo)排放。
(3)氮氧化物
磚瓦行業(yè)脫硝工作剛剛起步,行業(yè)內(nèi)應(yīng)開展低氮燃燒技術(shù)研究,通過改進(jìn)焙燒工藝,降低熱力型氮氧化物的產(chǎn)生。
磚瓦企業(yè)可以借鑒陶瓷行業(yè)的脫硝技術(shù)思路。陶瓷噴霧干燥塔:煙氣脫硝主要采用選擇性非催化還原技術(shù)(SNCR),少數(shù)企業(yè)采用濕法多污染物協(xié)同控制技術(shù)。陶瓷窯:煙氣脫硝難度大,陶瓷窯熱煙氣用于坯體干燥后,排煙溫度只有200℃左右,正在開發(fā)中低溫SCR技術(shù)。爐內(nèi)SNCR噴氨處理對陶瓷磚品質(zhì)有影響,應(yīng)用受到限制。目前可能的方法是采取濕法多污染物協(xié)同控制技術(shù),該技術(shù)在珠三角地區(qū)陶瓷企業(yè)已有工程應(yīng)用。過程控制:通過改進(jìn)燃燒設(shè)備和陶瓷原料配方,降低燒成溫度等過程控制技術(shù)也能降低NOx濃度。
磚瓦企業(yè)可以采取的脫硝技術(shù)有:
①過程控制:通過改進(jìn)燃燒設(shè)備和原料配方,降低燒成溫度、延長焙燒時間等降低NOx濃度(可以實(shí)現(xiàn))。
②煙氣脫硝:采用選擇性非催化還原技術(shù)(SNCR)(有條件實(shí)現(xiàn))。
③煙氣脫硝:采用濕法多污染物協(xié)同控制技術(shù)(氧化法脫硝,效率較低,氧化劑難以保存,有個別應(yīng)用)。
④煙氣脫硝:開發(fā)中低溫SCR技術(shù)(難度很大,其他行業(yè)有應(yīng)用)。
山東新澤儀器有限公司的煙氣在線監(jiān)測系統(tǒng),所有探頭、采樣系統(tǒng)部件都采用耐腐蝕材料,其中,探頭材質(zhì)為特種耐酸不銹鋼(316L) 、過濾器材質(zhì)為陶瓷、采樣伴熱管線為特別定制的Φ8聚四氟乙烯伴熱管。取樣探頭通過加熱器加熱到120℃~150℃,防止樣氣在經(jīng)過取樣探頭后,產(chǎn)生冷凝水。來自采樣探頭的樣氣經(jīng)高溫伴熱管線,通過三級過濾器除塵,經(jīng)過兩級冷凝系統(tǒng)除水后直接進(jìn)入分析儀內(nèi)測量。保證氣體測量的精準(zhǔn)性,設(shè)備的耐用性!
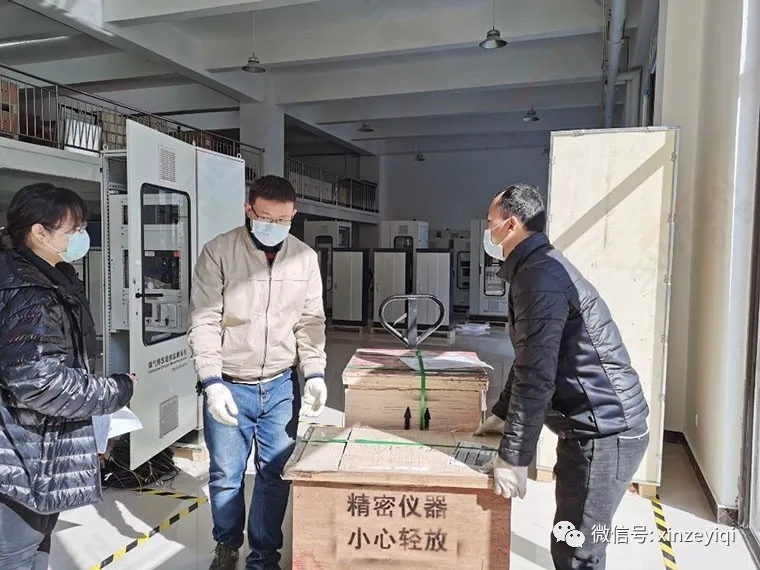